Ecolregul
Programmable shrink-wrapper : Shrink-wrapping and packaging
The shrink-wrapper is part of a packaging and wrapping process. It is used to group together various products in order to make them more
easier to handle and transport.
A rodless pneumatic cylinder selects the box arriving from the case packer and transfers it at 90° to the wrapping station.
the film-wrapping station. The box is held in place by a pneumatic cylinder while a second cylinder operates the film application and sealing unit
the film. The assembled batch, conveyed by a belt conveyor, passes through a PID-controlled hot air shrink oven. The effect of the heat (approx. 160°) causes the film to shrink around the cans. On leaving the oven, the batch is received and placed in a waiting area in the open air (cooling).
The technologies used on the EcolRégul shrink-wrapper are electric, pneumatic and electronic, which makes it possible to obtain a complete didactic approach
approach.
The EcolRegul system is a station of our EcolPlast production line.
Concept(s) associé(s)
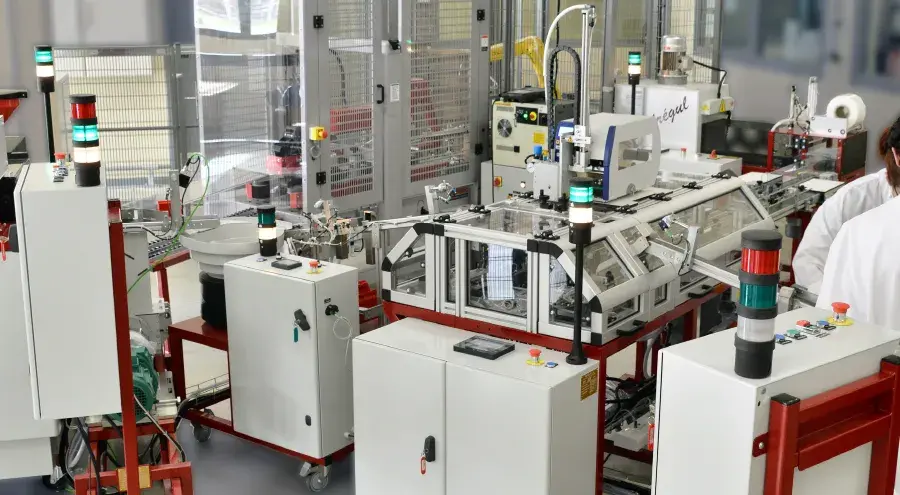
ECOLPLAST
Automated production line combining modularity and scalability
<p>This industrial line was designed by our design office, in collaboration with teaching teams, based on a real production and transformation line for plastic materials. </p> <p><br /> Ecolplast ensures the production and packaging of plastic parts, such as caps, customisable tokens (checkers, shopping cart tokens, etc.).<br /> The moulded parts are made by hot injection under pressure of polyethylene or polypropylene in the form of granules. A continuous part control by digital imaging allows the rejection of defective parts.</p> <p><br /> The production line systems then pack the parts into boxes, shrink-wrap the boxes and place them in cartons or plastic crates. The latter are evacuated onto a line exit conveyor which can be equipped to close the boxes using an industrial taping machine.</p> <p><br /> An associated system allows the recycling of sprues and rejects in order to reuse the raw material and optimise manufacturing costs. It also crushes plastic caps for integration into production. The line is composed of autonomous and independent systems that are combined to form a set of 4 to 9 stations, with control and supervision on PC and tablet.</p>