Mechanical engineering/industrial maintenance and line control
.webp)
EcolCafé
Production line 4.0, connected, integrated in a connected company.
<p style="text-align:justify">Industry 4.0 brings many benefits in terms of productivity and quality by transforming the factory into a global, interconnected system, in which the various systems communicate permanently.<br /> Maintenance has also undergone a profound transformation.<br /> At the heart of "Connected Production Systems Maintenance", curative, preventive and predictive maintenance are based on diagnostic tools assisted by digital technologies.<br /> Virtual reality is used to train technicians before they go on site, while augmented reality assists them in maintenance operations, where the operator equipped with 3D glasses is guided in real time by an avatar and has real-time access to data from the information systems.</p> <p style="text-align:justify">Advantage of this concept:<br /> An original pedagogy around 4.0 technologies within an evolving concept, based on a real production<br /> Respect for the environment through the use of recyclable consumables made of corn starch for local roaster production<br /> A system that is self-financing thanks to the internal consumption of coffee in the establishments</p>
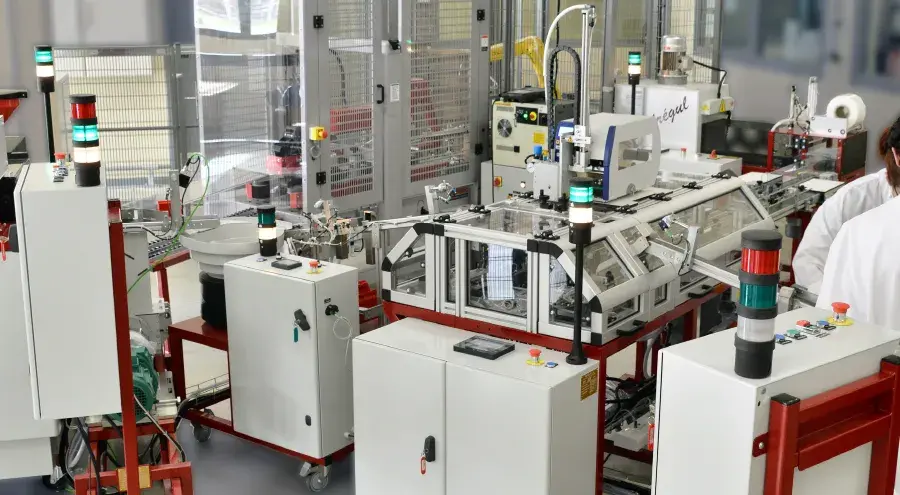
ECOLPLAST
Automated production line combining modularity and scalability
<p>This industrial line was designed by our design office, in collaboration with teaching teams, based on a real production and transformation line for plastic materials. </p> <p><br /> Ecolplast ensures the production and packaging of plastic parts, such as caps, customisable tokens (checkers, shopping cart tokens, etc.).<br /> The moulded parts are made by hot injection under pressure of polyethylene or polypropylene in the form of granules. A continuous part control by digital imaging allows the rejection of defective parts.</p> <p><br /> The production line systems then pack the parts into boxes, shrink-wrap the boxes and place them in cartons or plastic crates. The latter are evacuated onto a line exit conveyor which can be equipped to close the boxes using an industrial taping machine.</p> <p><br /> An associated system allows the recycling of sprues and rejects in order to reuse the raw material and optimise manufacturing costs. It also crushes plastic caps for integration into production. The line is composed of autonomous and independent systems that are combined to form a set of 4 to 9 stations, with control and supervision on PC and tablet.</p>
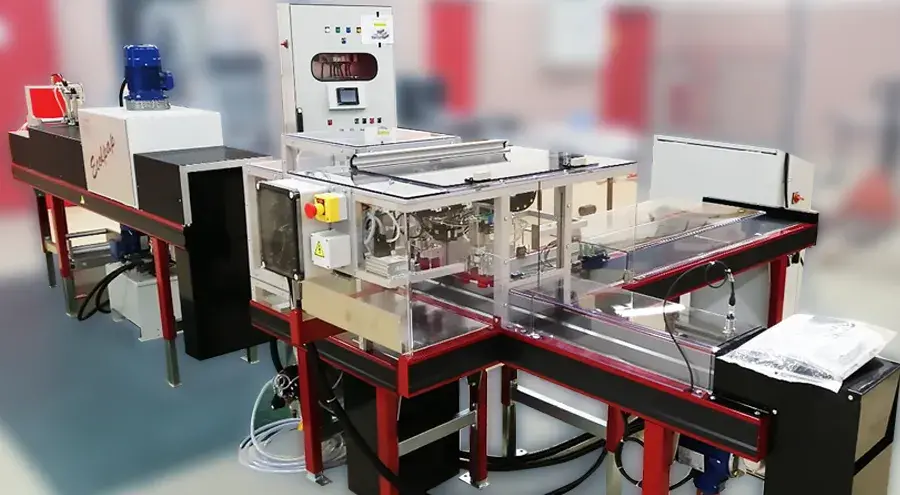
EcolProd
Supervised production workshop A complete production process
<p style="text-align:justify">EcolProd is an educational workshop with a complete production process. Initially, the raw material is paper and/or wood chips in the form of briquettes, or wooden briquettes and the final product is a packaged and stored cardboard. It consists of several independent stations (from 1 to 4 independent stations). The energy used is electrical, pneumatic and hydraulic. Different types of automatons, communication by supervision.</p> <p style="text-align:justify">It allows to consider several operating modes: Preparation operation, Production all the same, Closing operation. This workshop manages two types of briquettes as well as two types of briquette packs and two types of cartons: paper briquettes (adjustable dimensions H. 20 to 50 mm), wood briquettes (fixed dimensions H. 20 to 50 mm), pack of one briquette, pack of two briquettes, carton of four briquettes per layer, carton of six briquettes per layer.</p>